133 — Direktlink
08.11.2020, 14:29 Uhr
thomsen
|
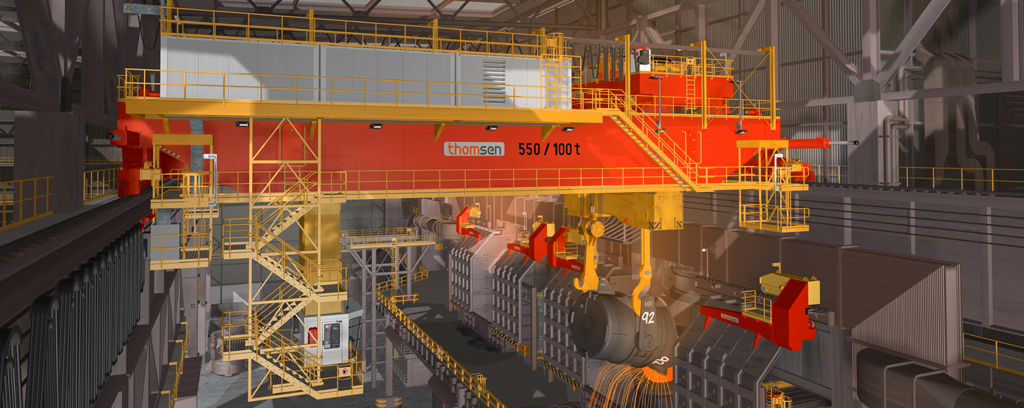
Zum eigentlichen Kran : Hier dargestellt ist ein Roheisen- Chargierkran als 4- Träger (Brücken-) Laufkran, abgebildet beim Befüll- (Chargier-) Vorgang des vorderen Konverters. Spurweite : 35.40 m, OK Kranschiene : 30.20 m, UK Dachbinder (Pultdach) etwa 42.10 m bis 43.60 m. Tragfähigkeit am Haupthub max. 550 t, Tragfähigkeit am Hilfshub max. 100 t. Ein weiterer, möglicher Reparaturzug ist hier nicht dargestellt.
Der Kran wurde nach bewährter Manier komplett „scratch“ gebaut - will heißen, ohne Vorlage von Konstruktionsunterlagen, Maßblättern etc. - hilfreich war jedoch eine Abbildung eines 4- Träger Laufkrans der Fa. Cone- Cranes im weltweiten Netz, an der ich mich weitgehend orientiert habe. Der hier dargestellte Kran trägt jedoch das Logo der weitestgehend unbekannten, da fiktiven Firma „Thomsen- Hüttentechnik“ ... 
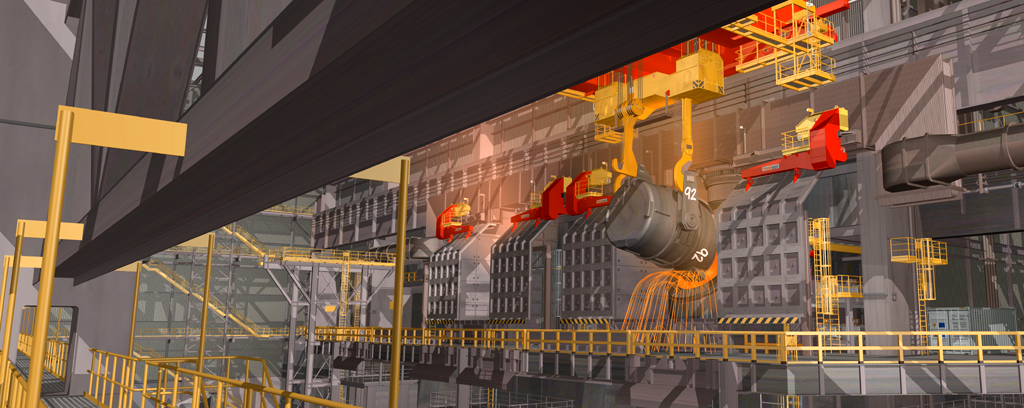
Ausblick vom sog. „Besucherlaufsteg“ von der der Konverterbühne gegenüberliegenden Stützenreihe. Der Laufsteg liegt in etwa auf der gleichen Höhe über OK Hallenboden wie die Konverterbühne und dient nicht nur der Führung von angemeldeten Besuchergruppen, sondern dient dem Betrieb auch als Zugang auf Anlagen, die zur Behandlung des flüssigen Stahls erforderlich sind, wie beispielsweise Abschlackständen, Argonspülen etc.
Ganz links im Vordergrund kann man die Führung des Steges durch die großen Kastenstützen erkennen, die neben dem Hallendach u.a. auch die Kranbahnträger für den dargestellten Chargierkran tragen. Rechts davon ist teilweise ein Treppenabgang auf eine der o.a. Behandlungsanlagen und weiter hinab auf Hüttenflur zu sehen. Der Laufsteg selbst ist hier von einem großen Fachwerkträger abgehängt.
Egal, ob ein Stahlwerkskomplex (nur das eigentliche Stahlwerk - gemeint ist hier nicht das ganze Hüttenwerk) aus der Historie „gewachsen“ ist (ggf. auch unter Einbeziehung vorhandener Hallenschiffe, die z.B. vormals dem Betrieb eines „Siemens- Martin“- Stahlwerks als technologischer Vorläufer dienten), oder „aus einem Guss“ geplant worden ist, wird der Hallenkomplex aus mehreren Hallenschiffen gebildet, die in ihrem Namen auch (meistens) die jeweilige Funktion tragen. Beispielsweise kann es die Schrotthalle geben, die Schlackenhalle, die Konverterhalle, die Mischerhalle (wobei vorhandene Roheisenmischer bereits vor vielen Jahren sämtlich demontiert worden sind, da sie in ihrer Funktion mittlerweile nicht mehr benötigt werden), die Einsetzhalle, die Konverterhalle, die Zustellhalle (die z.B. für weiter oben bereits skizzierte Zustellungen von Pfannen und Vacuumgefäßen von z.B. RH- Anlagen benötigt wird), die Gießhalle (wobei der Guß des flüssigen Stahls in Kokillen bereits vor Jahrzehnten durch Stranggussanlagen abgelöst wurde) und die Stripperhalle, in welcher die Kokillen nach dem Erstarren des Stahls mit einem Stripperkran von den Blöcken abgezogen worden sind.
In den beiden letztgenannten Hallenschiffen können heutzutage dann z.B. moderne Anlagen der „Sekundärmetallurgie“ ihren Platz finden, wie z.B. Stahlentgasungsanlagen, Pfannenöfen, Argonspülen etc. Dort wird der flüssige Rohstahl aus den Konvertern entsprechend den geforderten technologischen Eigenschaften weiterbehandelt, bevor er in einer nachgeschalteten Stranggußanlage zu einem „Endlos“- Strang vergossen werden kann und abschließend in Rohbrammen geteilt wird. Die Rohbrammen können dann in Längs- und Querteilanlagen nach Bedarf weiter geteilt werden. Ferner können dort Lager- und Werkstattflächen der unmittelbar benachbarten Stranggussanlage und des Oxygenstahlwerkes eingerichtet sein.
In der o.a. Mischerhalle kann heutzutage beispielsweise eine Roheisen- Vorentschwefelung angeordnet sein, die dem Prozess im Konverter vorgeschaltet ist. Die Mischer sind nicht mehr erforderlich, da die Prozessleittechnik der Hochöfen in den letzten Jahren und Jahrzehnten fortentwickelt und immer weiter modernisiert worden ist, so dass die Roheisenqualität und Zusammensetzung mittlerweile so gleichmäßig ist, dass ein Vergleichmäßigen in den Mischergefäßen entfallen kann. Zudem kann das flüssige Roheisen in den wärmegedämmten und mit 2 Lagen ff- Material (Dauerfutter und Verschleißfutter) ausgekleideten „Torpedowagen“ nicht nur von A nach B transportiert werden, sondern auch über viele Stunden ohne nennenswerte Temperaturverluste flüssig gehalten werden, so dass auch die Puffer- und Bevorratungsfunktion der Roheisenmischer nicht mehr benötigt wird. Ferner können in der Mischerhalle die Roheisenumfüllgruben angeordnet sein, wo das in den Torpedowagen von den Hochöfen angelieferte Roheisen in Gieß- und Transportpfannen umgefüllt wird.
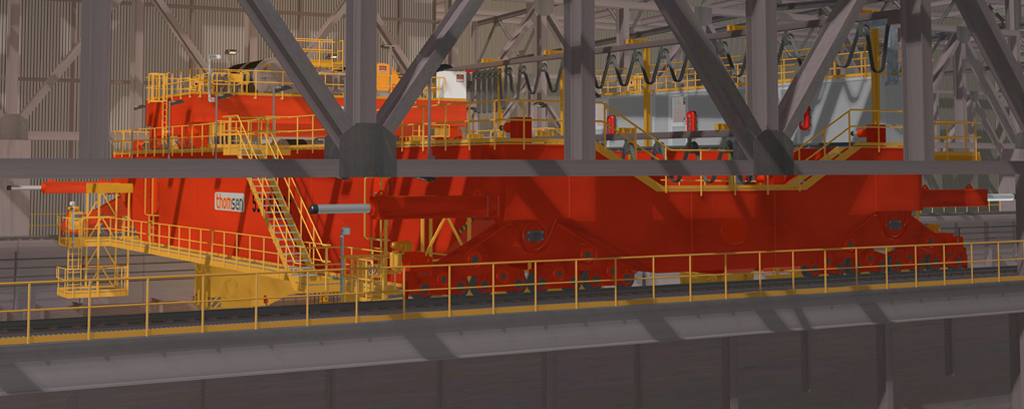
Der Chargierkran geht seiner Arbeit hoch oben unter dem Hallendach nach, so dass er hier und da von Bauteilen der Halle verdeckt wird, und kaum in Gänze gezeigt werden kann.
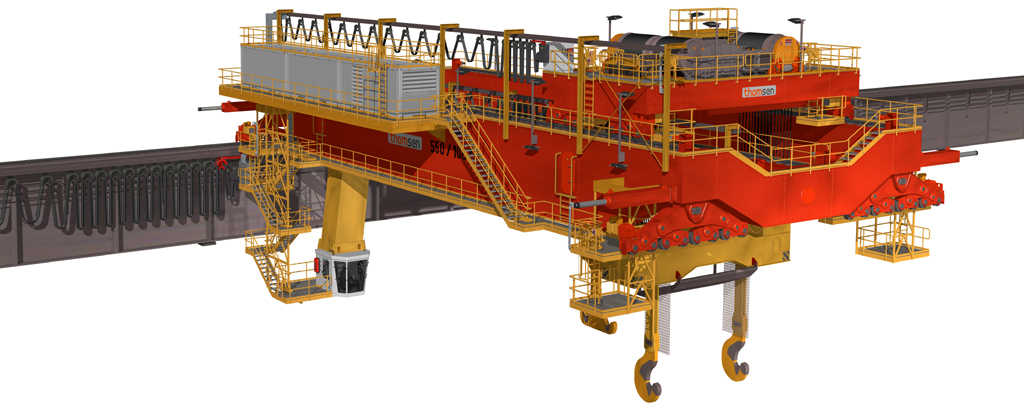
Die folgenden Abbildungen zeigen den Kran daher weitgehend bzw. komplett losgelöst von seiner Umgebung. Nach einer gewissen Betriebszeit im Oxygenstahlwerk ist dort übrigens Alles - und ich meine Alles - von einer hellgrauen Staubschicht bedeckt. Da man grau auf grau schlecht unterscheiden kann, habe ich den Kran und einige Bauteile farblich differenziert von seiner Umgebung dargestellt. Gehen wir also davon aus, dass es sich hier um einen neuen Kran handelt. Nichts hält ewig - auch wenn der Kran korrekt geplant und gefertigt wurde, ist auch die beste Konstruktion irgendwann einmal ermüdet und muss erneuert werden.
Zur Verdeutlichung : Im optimalen Falle kann man für das Befüllen eines Konverters mit Schrott und Roheisen, den eigentlichen Blasprozess und die anschließende Entleerung des Rohstahls in Transportpfannen und das abschließende Abgießen der Schlacke in Schlackenpfannen etwa 40 bis 45 Minuten ansetzen, bevor wieder erneut befüllt werden kann. Dieses Zeitfenster eines „Arbeitsspiels“ wird auch als „tap- to- tap“- Zeit bezeichnet. Arbeiten beide Konverter bei guter Konjunktur im Wechsel, dann kann etwa alle 20 bis 30 Minuten ein Konverter befüllt werden - also bis zu 3 mal in der Stunde. Bei einer weiter oben bereits skizzierten Bruttolast von etwa 500 t x 3 mal in der Stunde x 24 Stunden bei Dreischichtbetrieb können so von dem Chargierkran pro Arbeitstag theoretisch maximal etwa 36.000 t Last bewegt werden. Diese Zahl in der Praxis zu erreichen erscheint mir dann doch etwas zu theoretisch, da dann natürlich die An- und Abfuhr - sprich die Anlieferung von Roheisen und die Weiterverarbeitung bis hin zur Rohbramme - lücken- und pausenlos gewährleistet sein muss und in der gleichen Zeit synchronisiert zu den Arbeitszeiten der Konverter verarbeitet werden muss. Auch kleinere Betriebsunterbrechungen wie Konvertermundputzen, Heißreparaturen mit Spritzmassen etc. dürften dann nicht erfolgen.
Am Kranbahnträger sind die Stromkabelschlaufen zu sehen, die dort an einem Träger oder in einer Helmschiene über mittels Rollen verschiebbare Sättel geführt werden und je nach Standort des Krans recht weit voneinander ausgezogen worden sind oder im sog. „Kabelbahnhof“ in Parkposition dicht aneinander geschoben worden sind.
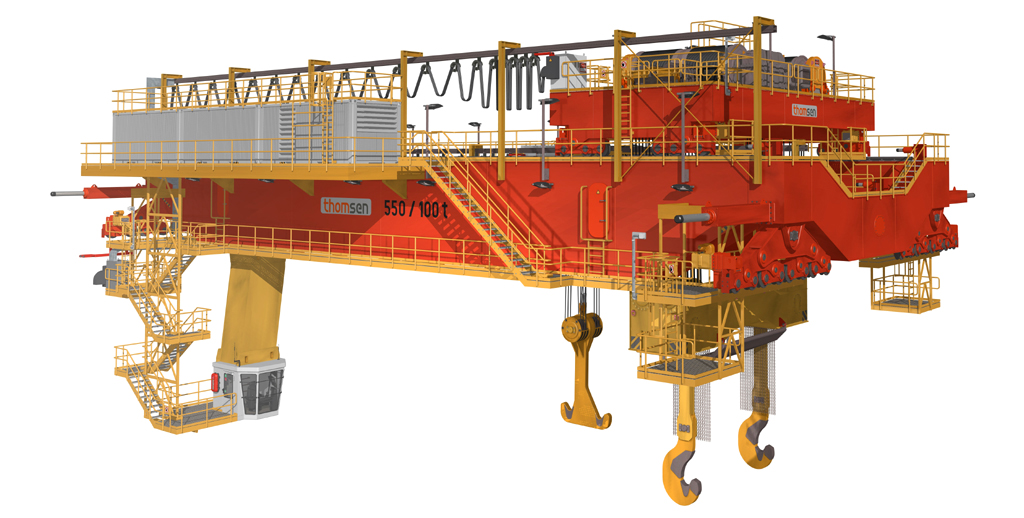
Links oben im Bild ist eine Reihe von drei 20- Fuß- Containern zu erkennen, wobei der Container ganz links und der in der Mitte Schaltraumcontainer darstellen, in denen die erforderliche Elektrotechnik staubgeschützt und klimatisiert untergebracht ist. Rechts der Container mit den Lüftungsjalousien beinhaltet die obligatorische und erforderliche Lüftungs- bzw. Klimaanlage, damit die entstehende, unvermeidliche Verlustwärme der E- Technik weggekühlt werden kann. Bekanntlich gehen elektrische Schaltanlagen nur bis zu einer gewissen Temperatur ihrer Arbeit zuverlässig nach - bei zu warmen Schalträumen muss dann ggf. mit Ausfällen der Elektrik gerechnet werden - was bei einem solchen Schlüsselgerät schnell fatal werden kann, und das nicht nur in finanzieller Hinsicht.
01 von 07 -- Wir bauen auf und reissen nieder, so haben wir Arbeit - immer wieder ! |